Welcome to My Blog!
Before we dive into the content, I’d love for you to join me on my social media platforms where I share more insights, engage with the community, and post updates. Here’s how you can connect with me:
Facebook:https://www.facebook.com/profile.php?id=61567891941530
Now, let’s get started on our journey together. I hope you find the content here insightful, engaging, and valuable.
Caisu Machinery sells a variety of used plastic pipe production equipment. The products are of high quality and low price. Welcome to contact us for consultation and purchase. We will be happy to serve you.
Table of Contents
Introduction
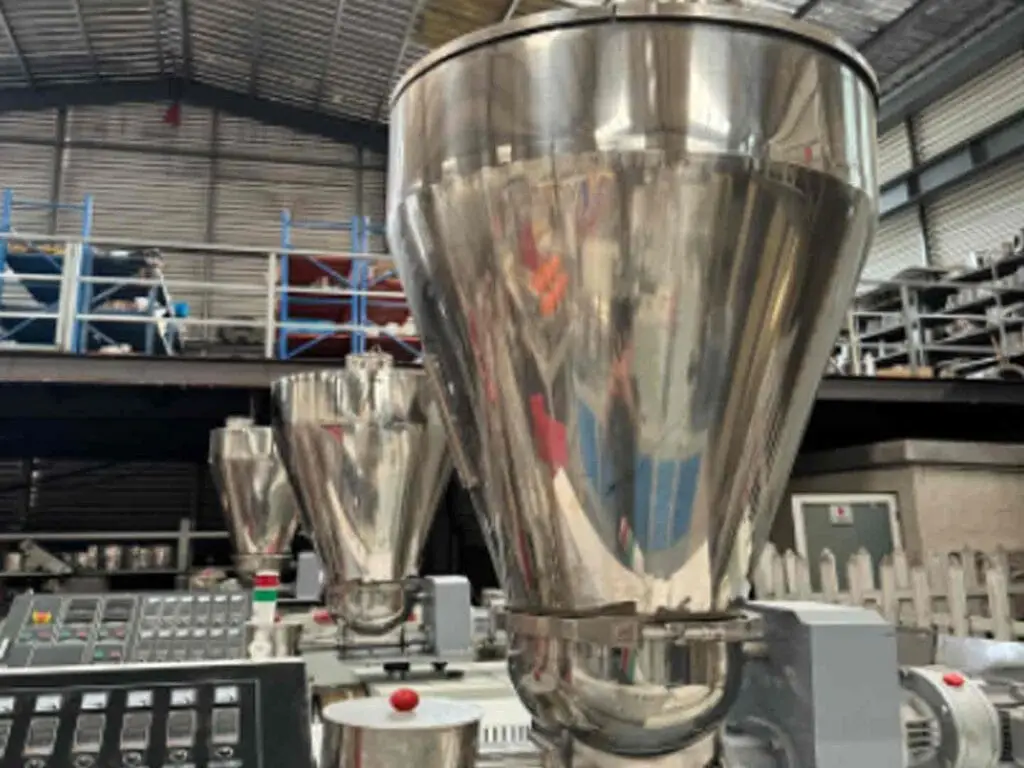
Screw extruders are essential machines in various industries, including plastic processing, food production, and pharmaceutical manufacturing. They are used to process raw materials by applying heat, pressure, and mechanical shearing to create a continuous flow of shaped products. Depending on the industry and application, different types of screw extruders are used, each offering unique advantages and processing capabilities.
This article explores the various types of screw extruders, their working principles, and their applications. A comparative table is included to highlight key differences between the different types of screw extruders. Additionally, the article provides insights into the advantages, challenges, and frequently asked questions about screw extruders.
What is a Screw Extruder?
A screw extruder is a mechanical device that uses one or more rotating screws within a barrel to transport, mix, and shape materials. The main components of a screw extruder include:
- Hopper: Where raw materials are fed into the extruder.
- Screw and Barrel: The core components responsible for conveying, melting, and homogenizing the material.
- Heating and Cooling System: Maintains the required processing temperature.
- Die: Shapes the final extruded product.
- Drive System: Provides the necessary torque to rotate the screw.
Screw extruders are widely used in polymer processing, food extrusion, and industrial material production due to their efficiency and versatility.
Types of Screw Extruder
Single-Screw Extruder
The single-screw extruder is the most common type used in industries such as plastic molding, food production, and pharmaceutical processing. It consists of a single rotating screw inside a heated barrel.
Advantages:
- Simple design and easy operation
- Cost-effective for standard processing
- Suitable for continuous production
Common Applications:
- Plastic extrusion (pipes, sheets, and films)
- Food processing (snack foods, pasta)
- Pharmaceutical applications (pellet production)
Twin-Screw Extruder
The twin-screw extruder features two intermeshing screws inside the barrel, providing better mixing, heat transfer, and processing stability. It can be either co-rotating or counter-rotating, depending on the application.
Advantages:
- Higher mixing efficiency and material homogeneity
- Greater flexibility in processing different materials
- Enhanced heat and mass transfer
Common Applications:
- High-performance plastic compounding
- Food extrusion (protein-based products, cereals)
- Pharmaceutical drug formulation
Co-Rotating Twin-Screw Extruder
In a co-rotating twin-screw extruder, both screws rotate in the same direction, creating a strong shearing and mixing effect. This type is commonly used for compounding and polymer processing.
Advantages:
- Excellent mixing and dispersion properties
- Faster material processing
- Suitable for advanced polymer applications
Common Applications:
- Engineering plastics and masterbatch production
- Biodegradable plastics
- Food and feed processing
Counter-Rotating Twin-Screw Extruder
Counter-rotating twin-screw extruders have screws that rotate in opposite directions. They are often used for PVC pipe and profile extrusion due to their ability to handle heat-sensitive materials effectively.
Advantages:
- Lower shear stress on materials
- Ideal for heat-sensitive polymers
- Precise processing control
Common Applications:
- PVC pipe and profile manufacturing
- Cable insulation extrusion
- Wood-plastic composite production
Multi-Screw Extruder
Multi-screw extruders, such as triple-screw and quad-screw extruders, are designed for highly specialized applications requiring superior mixing and reaction control.
Advantages:
- Improved processing of complex materials
- Higher throughput rates
- Enhanced energy efficiency
Common Applications:
- High-end polymer blending
- Specialty food processing
- Pharmaceutical active ingredient dispersion
Comparison of Different Screw Extruders
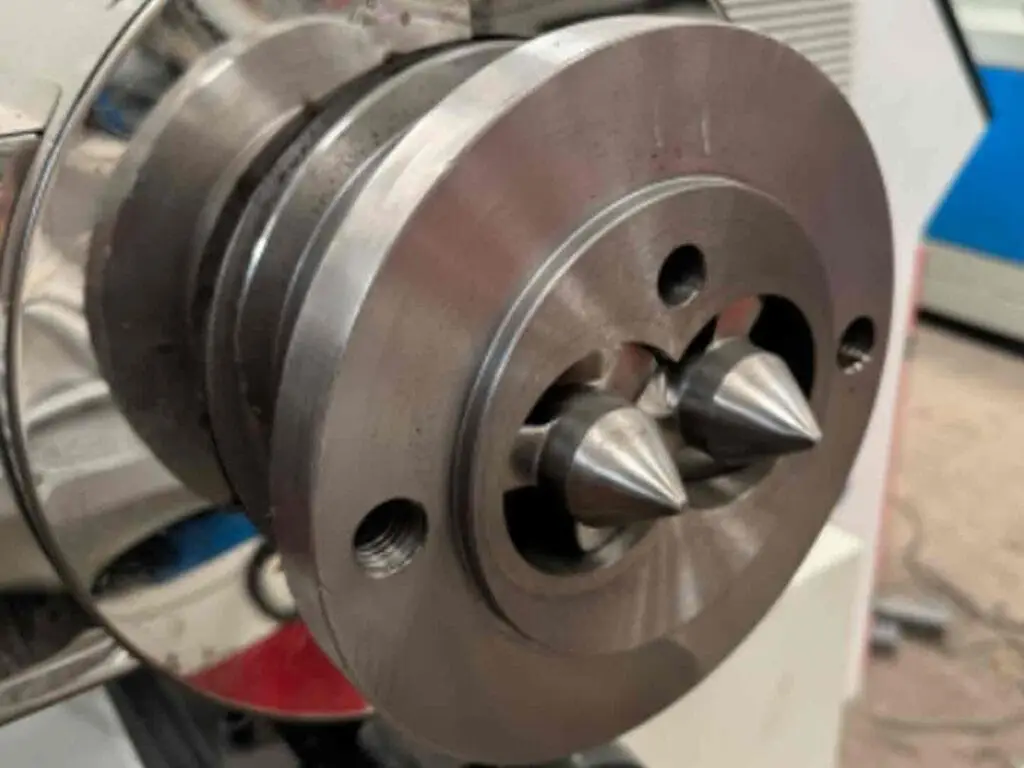
Type of Screw Extruder | Number of Screws | Mixing Efficiency | Shear Rate | Common Applications |
---|---|---|---|---|
Single-Screw Extruder | 1 | Moderate | Medium | Plastic extrusion, food processing, pharmaceuticals |
Twin-Screw Extruder | 2 | High | High | Polymer compounding, food extrusion, pharmaceuticals |
Co-Rotating Twin-Screw Extruder | 2 | Very High | High | Engineering plastics, masterbatch production, biodegradable plastics |
Counter-Rotating Twin-Screw Extruder | 2 | Moderate | Low | PVC pipe extrusion, wood-plastic composites, cable insulation |
Multi-Screw Extruder | 3+ | Very High | Adjustable | Advanced polymer blending, pharmaceutical applications, specialty food processing |
Applications of Screw Extruders in Different Industries
Plastic and Polymer Industry
Screw extruders are widely used in the production of plastic pipes, sheets, films, and granules. They ensure precise control over material composition and product quality.
Food Industry
In food processing, screw extruders play a critical role in producing pasta, breakfast cereals, textured vegetable proteins, and snack foods. They help achieve the desired texture and consistency in food products.
Pharmaceutical Industry
Screw extruders are used in drug formulation and controlled-release medications. They enable uniform dispersion of active pharmaceutical ingredients (APIs) in polymer matrices.
Chemical and Industrial Applications
Screw extruders are utilized for processing adhesives, sealants, and coatings. They facilitate the efficient blending of chemical compounds for industrial applications.
Advantages of Screw Extruders
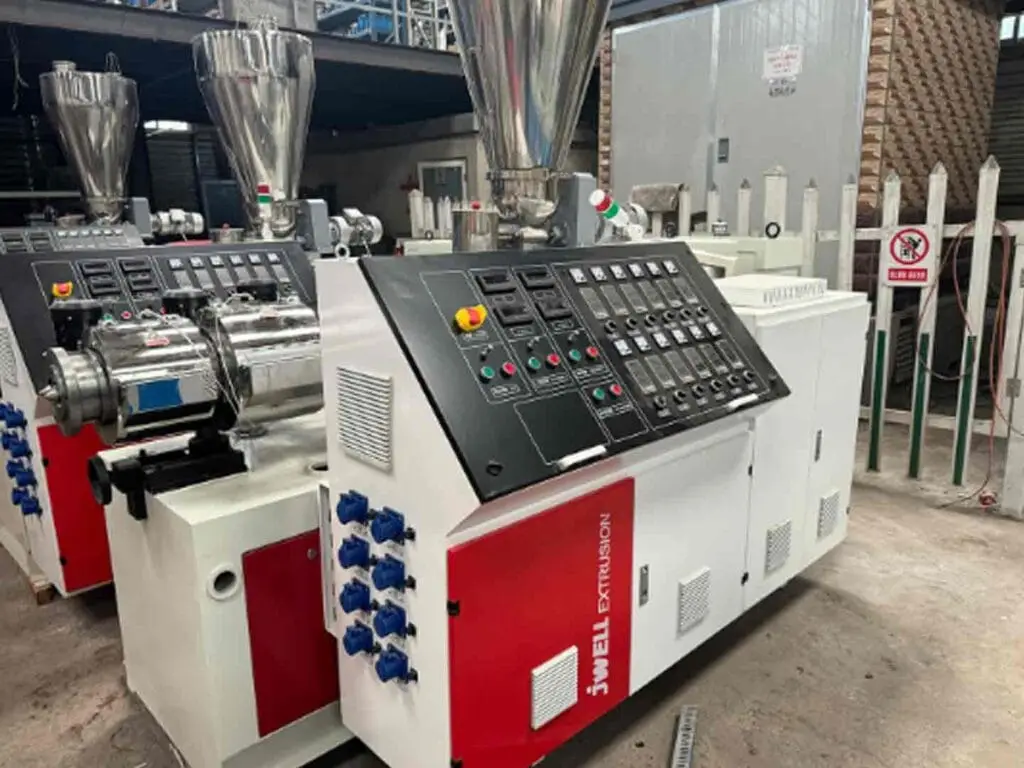
- Continuous Processing: Provides a steady output with minimal material waste.
- Energy Efficiency: Uses controlled heating and shearing mechanisms to optimize energy consumption.
- Versatility: Suitable for a wide range of materials, including plastics, food ingredients, and pharmaceutical compounds.
- High-Quality Products: Ensures uniform mixing, melting, and shaping of materials.
Conclusion
Screw extruders are vital machines in multiple industries, offering efficient processing capabilities for polymers, food, pharmaceuticals, and industrial materials. The choice of a screw extruder depends on the application requirements, material properties, and desired production output.
From single-screw extruders for basic applications to twin-screw and multi-screw extruders for complex processing needs, these machines continue to evolve, providing advanced solutions for modern manufacturing. As industries demand higher efficiency and product quality, screw extruders will play an increasingly significant role in material processing.
FAQ
What is the difference between a single-screw and twin-screw extruder?
A single-screw extruder is simpler and cost-effective, while a twin-screw extruder offers better mixing, higher efficiency, and improved processing control.
Which type of screw extruder is best for PVC processing?
Counter-rotating twin-screw extruders are ideal for PVC pipe and profile extrusion due to their low shear and precise temperature control.
Can screw extruders be used for food production?
Yes, screw extruders are commonly used in food processing for producing pasta, snacks, and protein-based food products.
What industries use screw extruders?
Screw extruders are used in plastics, food, pharmaceuticals, chemicals, and other industrial applications requiring material extrusion.
How do I choose the right screw extruder for my application?
Consider factors such as material type, processing temperature, required output, and mixing efficiency to determine the most suitable screw extruder.