Welcome to My Blog!
Before we dive into the content, I’d love for you to join me on my social media platforms where I share more insights, engage with the community, and post updates. Here’s how you can connect with me:
Facebook:https://www.facebook.com/profile.php?id=61567891941530
Now, let’s get started on our journey together. I hope you find the content here insightful, engaging, and valuable.
Caisu Machinery sells a variety of used plastic pipe production equipment. The products are of high quality and low price. Welcome to contact us for consultation and purchase. We will be happy to serve you.
Table of Contents
Introduction
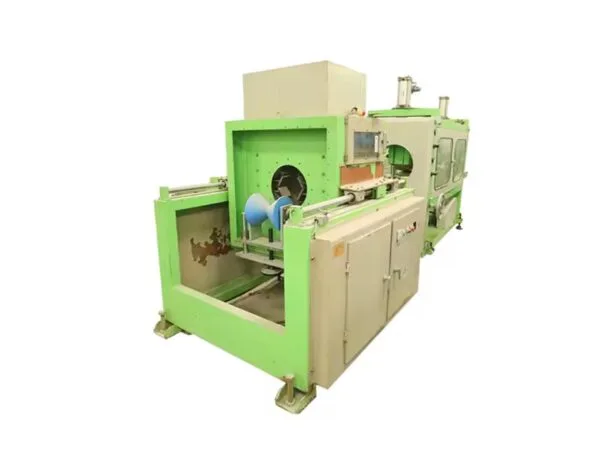
In the rapidly evolving world of plastics manufacturing, plastic pipe extrusion lines have become an essential tool for producing high-quality, durable, and versatile plastic pipes. Whether you are involved in construction, plumbing, irrigation, or industrial applications, understanding the intricacies of plastic pipe extrusion lines is crucial for making informed decisions.
This comprehensive guide will delve into the key components, features, and considerations when choosing plastic pipe extrusion lines. Whether you are a manufacturer, an engineer, or a business owner looking to invest in this technology, this blog will provide you with valuable insights into why plastic pipe extrusion lines are essential for modern production processes.
Understanding Plastic Pipe Extrusion Lines
Plastic pipe extrusion lines are specialized machines designed to produce plastic pipes through a continuous process. These lines consist of several key components, including extruders, dies, cooling systems, and pullers. The process involves melting plastic pellets, extruding the molten material through a die to form a pipe, and then cooling and solidifying the pipe to its final shape. Understanding the components and capabilities of plastic pipe extrusion lines is essential for optimizing production efficiency and ensuring high-quality output.
Key Components of Plastic Pipe Extrusion Lines
To fully grasp the functionality of plastic pipe extrusion lines, it is important to understand their key components:
Extruder
The extruder is the heart of the extrusion line, responsible for melting and mixing the plastic pellets. It typically consists of a barrel, screw, and heating elements. The screw design and barrel length can significantly impact the mixing and melting efficiency of the plastic material.
Die
The die is a critical component that shapes the molten plastic into a pipe. It must be precisely engineered to ensure uniform thickness and smooth surface finish of the pipe. The die design also affects the overall production speed and efficiency.
Cooling System
After the plastic is extruded through the die, it needs to be cooled and solidified. Cooling systems can include water baths, air cooling, or a combination of both. Proper cooling ensures that the pipe maintains its shape and dimensions without warping or shrinking.
Puller
The puller is responsible for pulling the cooled pipe through the extrusion line at a consistent speed. It ensures that the pipe is produced with uniform dimensions and prevents defects such as ovality or uneven thickness.
Cutting and Coiling Unit
Once the pipe is extruded and cooled, it needs to be cut to the desired length or coiled for storage and transportation. Cutting and coiling units are designed to handle various pipe sizes and materials, ensuring precise and efficient processing.
A Comprehensive Table of Plastic Pipe Extrusion Line Specifications
To provide a clearer understanding of plastic pipe extrusion lines and their capabilities, the following table summarizes key specifications:
Feature | Specification |
---|---|
Extruder Capacity | 20 – 200 kg/hour |
Pipe Diameter Range | 16 mm – 1,000 mm |
Pipe Wall Thickness | 1 mm – 50 mm |
Cooling Method | Water bath, air cooling, or combination |
Production Speed | 1 – 10 meters/minute |
Material Compatibility | HDPE, LDPE, PVC, PP, etc. |
Die Sizes | Customizable to meet specific requirements |
Power Consumption | 10 – 100 kW |
This table highlights the key characteristics of plastic pipe extrusion lines, emphasizing their versatility and suitability for a wide range of production needs.
Choosing the Right Plastic Pipe Extrusion Line
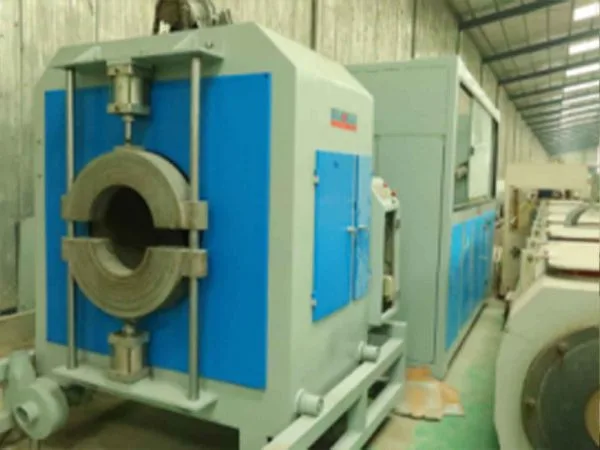
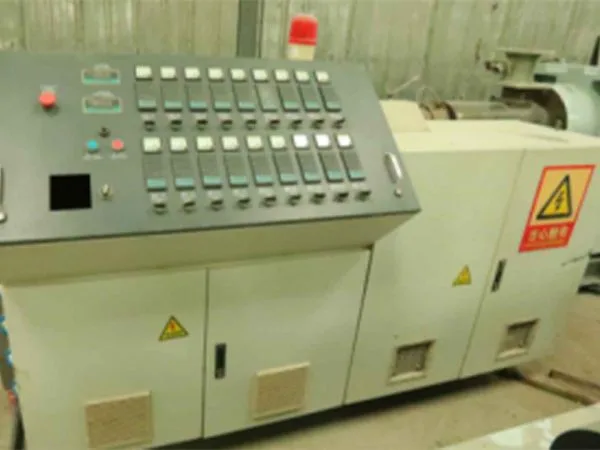
Selecting the best plastic pipe extrusion line for your production needs involves careful consideration of several factors:
Production Capacity
Determine the production capacity required based on your demand. Extrusion lines vary in capacity, ranging from small-scale production to high-volume manufacturing. Choose a line that can meet your current needs while allowing for future expansion.
Pipe Size and Material
Consider the range of pipe sizes and materials you plan to produce. Different extrusion lines are designed to handle specific pipe diameters and materials such as HDPE, LDPE, PVC, and PP. Ensure that the line you choose is compatible with your desired products.
Cooling System
The cooling system plays a crucial role in maintaining the quality and dimensions of the pipe. Water baths provide rapid and uniform cooling, while air cooling is more energy-efficient. Some lines offer a combination of both methods. Choose a cooling system that suits your production requirements and environmental considerations.
Automation and Control
Modern plastic pipe extrusion lines come with advanced automation and control systems that enhance efficiency, precision, and ease of operation. Look for features such as PLC controls, touch-screen interfaces, and real-time monitoring capabilities. These systems can help optimize production parameters, reduce downtime, and improve overall quality.
Maintenance and Support
Investing in a reliable extrusion line from a reputable manufacturer ensures that you have access to proper maintenance and support services. Consider the availability of spare parts, technical support, and after-sales service. Regular maintenance and timely repairs can significantly extend the lifespan of your equipment and reduce operational costs.
Advantages of Using Plastic Pipe Extrusion Lines
Plastic pipe extrusion lines offer several advantages that make them a preferred choice in the manufacturing industry:
High Production Efficiency
The continuous extrusion process allows for high production rates, making it suitable for large-scale manufacturing. The ability to produce pipes of various sizes and lengths in a single operation enhances overall efficiency and reduces production time.
Versatility in Pipe Sizes and Materials
Plastic pipe extrusion lines can handle a wide range of pipe diameters and wall thicknesses, making them highly versatile. They are also compatible with various plastic materials, allowing manufacturers to produce pipes with different properties and applications.
Consistent Quality
Modern extrusion lines are equipped with advanced control systems that ensure consistent quality throughout the production process. Precise temperature control, uniform cooling, and accurate die design contribute to producing pipes with uniform dimensions and smooth surfaces.
Cost-Effective
While the initial investment in a plastic pipe extrusion line can be significant, the long-term benefits make it a cost-effective solution. High production efficiency, reduced material waste, and lower labor costs contribute to a favorable return on investment.
Environmentally Friendly
Plastic pipes are lightweight, durable, and have a long lifespan, reducing the need for frequent replacements. Additionally, the extrusion process generates minimal waste, making it an environmentally friendly manufacturing option.
Future Trends in Plastic Pipe Extrusion Technology
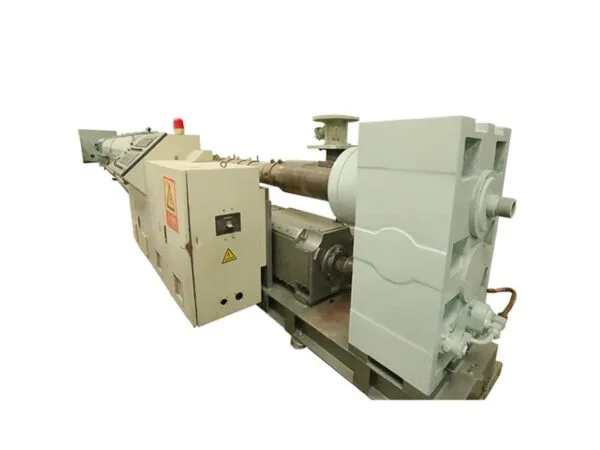
As technology continues to advance, plastic pipe extrusion lines are becoming more sophisticated and efficient. Innovations in extruder design, die technology, and cooling systems are enhancing production capabilities and improving product quality. Additionally, the integration of smart manufacturing technologies such as IoT, AI, and machine learning is revolutionizing the way extrusion lines operate. These advancements enable real-time monitoring, predictive maintenance, and optimized production processes, making plastic pipe extrusion lines more efficient and reliable than ever before.
Conclusion
Choosing the best plastic pipe extrusion line for your manufacturing needs involves careful consideration of key components, production capacity, pipe size and material, cooling systems, and automation features. By understanding these factors and evaluating your specific requirements, you can select a line that will enhance your production efficiency, ensure consistent quality, and provide long-term cost savings.
If you are looking to invest in a high-quality plastic pipe extrusion line, contact us today to explore our range of advanced and reliable solutions. Our team of experts will guide you through the options and help you choose the perfect extrusion line for your production needs.
FAQ
What are plastic pipe extrusion lines used for?
Plastic pipe extrusion lines are used for manufacturing plastic pipes of various sizes and materials. They are essential in industries such as construction, plumbing, irrigation, and industrial applications where durable and versatile pipes are required.
How do I choose the best plastic pipe extrusion line for my needs?
The key components include the extruder, die, cooling system, puller, and cutting or coiling unit. Each component plays a crucial role in the extrusion process, ensuring high-quality and consistent pipe production.
What are the key components of a plastic pipe extrusion line?
The key components include the extruder, die, cooling system, puller, and cutting or coiling unit. Each component plays a crucial role in the extrusion process, ensuring high-quality and consistent pipe production.
How do I ensure consistent quality with a plastic pipe extrusion line?
Modern extrusion lines come with advanced control systems that ensure consistent temperature, uniform cooling, and precise die design. These features contribute to producing pipes with uniform dimensions and smooth surfaces, enhancing overall quality.
What materials can be used with plastic pipe extrusion lines?
Plastic pipe extrusion lines are compatible with various materials such as HDPE, LDPE, PVC, and PP. The choice of material depends on the specific application and desired properties of the pipes.